Now I could finish modeling the front and back of the head.
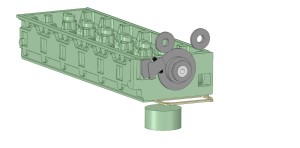
Next the front timing cover. The water outlet exits the head in the front and makes a 90 degree turn through the timing cover where the thermostat housing will mount. This design has been one away with as it was deemed that it wouldn’t provide enough flow for turbo cars. It was too late for this head though.
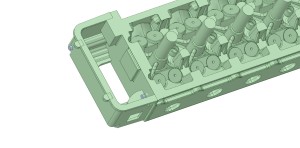
Now the valve cover. The K20 cam towers kind of dictated the overall size but I was still able to get the styling I was looking for. I was originally going to machine in the lettering but I put it to a vote and this design won out.
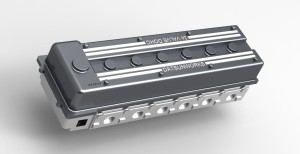
After talking with Jeff about his testing on coolant flow I decided to get the most out of the 3D sand printing process as I could. I designed a water jacket that would be pretty hard to duplicate traditionally. There is a lot of surface area so hopefully there will be large improvements in cooling.
Here is a nice shot of the intake and exhaust cores, water core, and upper tensioner. You can see where the cross drilling will go to supply oil to the head, tensioner and idler gear lube.
There will have to be additional oil supplied to the last three cam towers as the single feed in the front won’t cut it.
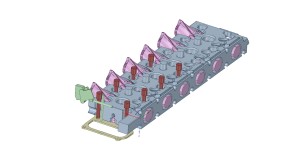
Here is a cross section of the head. The cut plane is through the center of one of the intake valves so the ports look a bit off. There is machine allowance on the bottom so the combustion chamber is a little larger than it will be after surfacing.
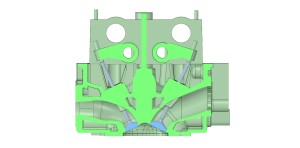
The design work on the head is pretty much done at this point so it’s time for mold design.