Today I was able to finish up the machine work on the timing cover and head.
The timing cover is a bit of a kludge as I had printed the mold before I fully finalized the timing cover. It works but it will be better in future versions. I had to get it cast and on the head so the machine shop could surface it all together.
Here I’ve mounted the cover to the front of the head, machined the surface flush with the bottom and drilled the front holes for the lower cover.
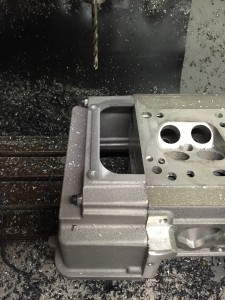
The front lip is a little thin. I’ll add material to the pattern to thicken it up. I really should have left more material around the entire head. That way I could have made a cleanup pass around the whole thing. I have enough material on the valve cover to create a lip to hide it so it will look good when it’s buttoned up. This head will have a water outlet on the side of the timing cover but future heads will use a coolant manifold like the OSG head.

Very happy with the internal fit. I need to rig something for the front cover bolts. The holes are right on the step. I’ll add bosses to the pattern so it won’t be a problem later on.
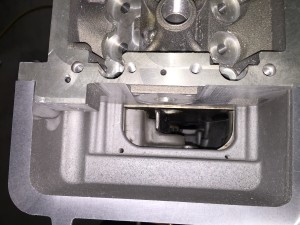
So I didn’t try to make it fit this well but the “as cast” fit between the factory cover and my cover couldn’t have been better. Of course it’s in a spot where no one will see it 
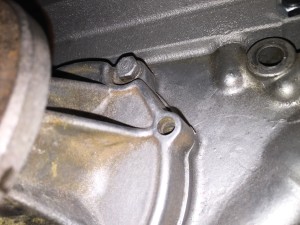
