Made the filter housings today. They use the same wire mesh and oiled foam filters that I use on my other manifold. I’ve been very happy with the filtration from the foam and saw no reason to do anything different. The housing probably isn’t the best choice for power as it will disturb the air flow around the bell. Meh who cares. I like the look.
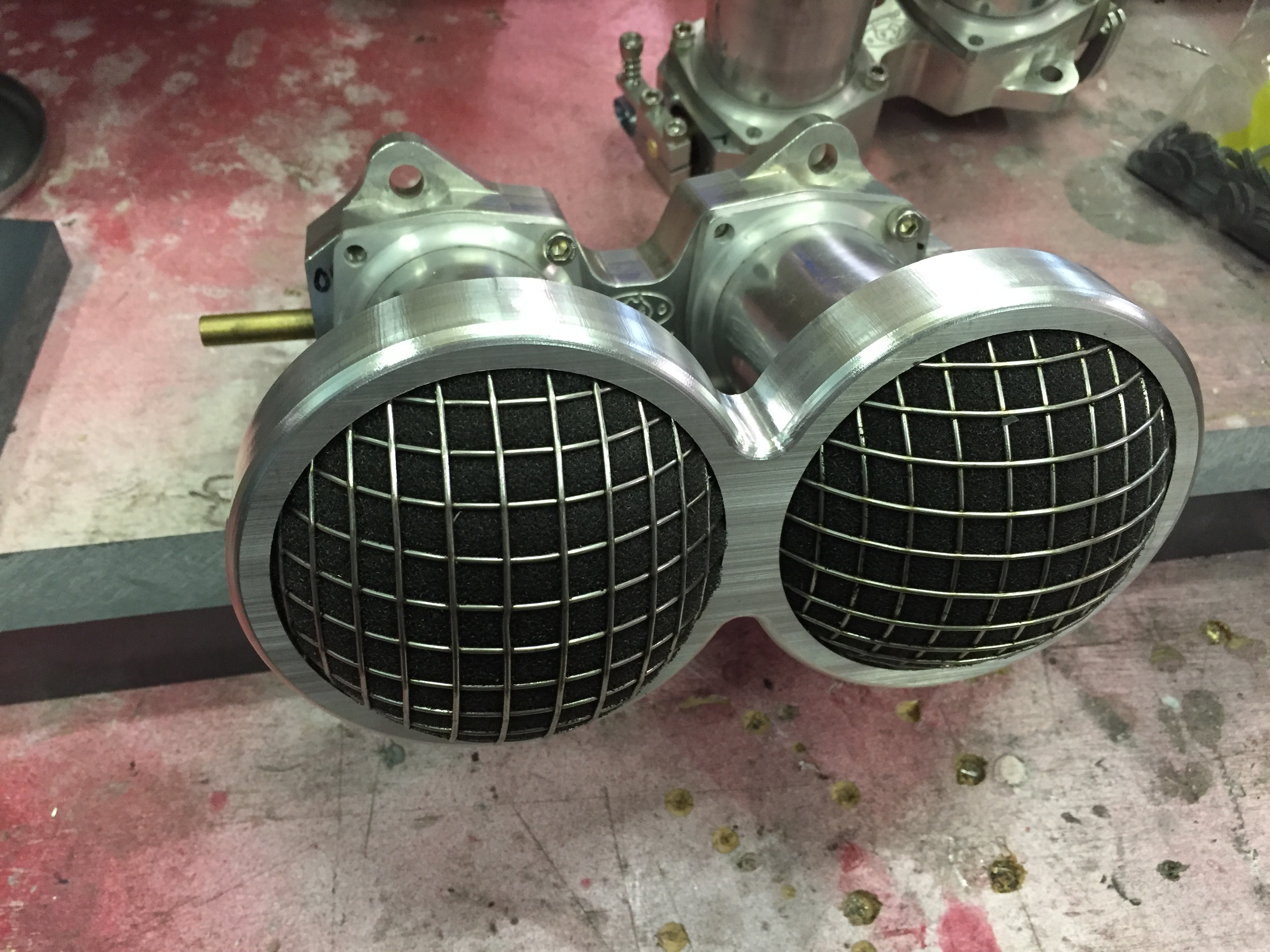
They still need finishing so the tooling marks from a well used CNC mill are visible.
I have a little boss on either side that will hold a set screw to hold them in place.
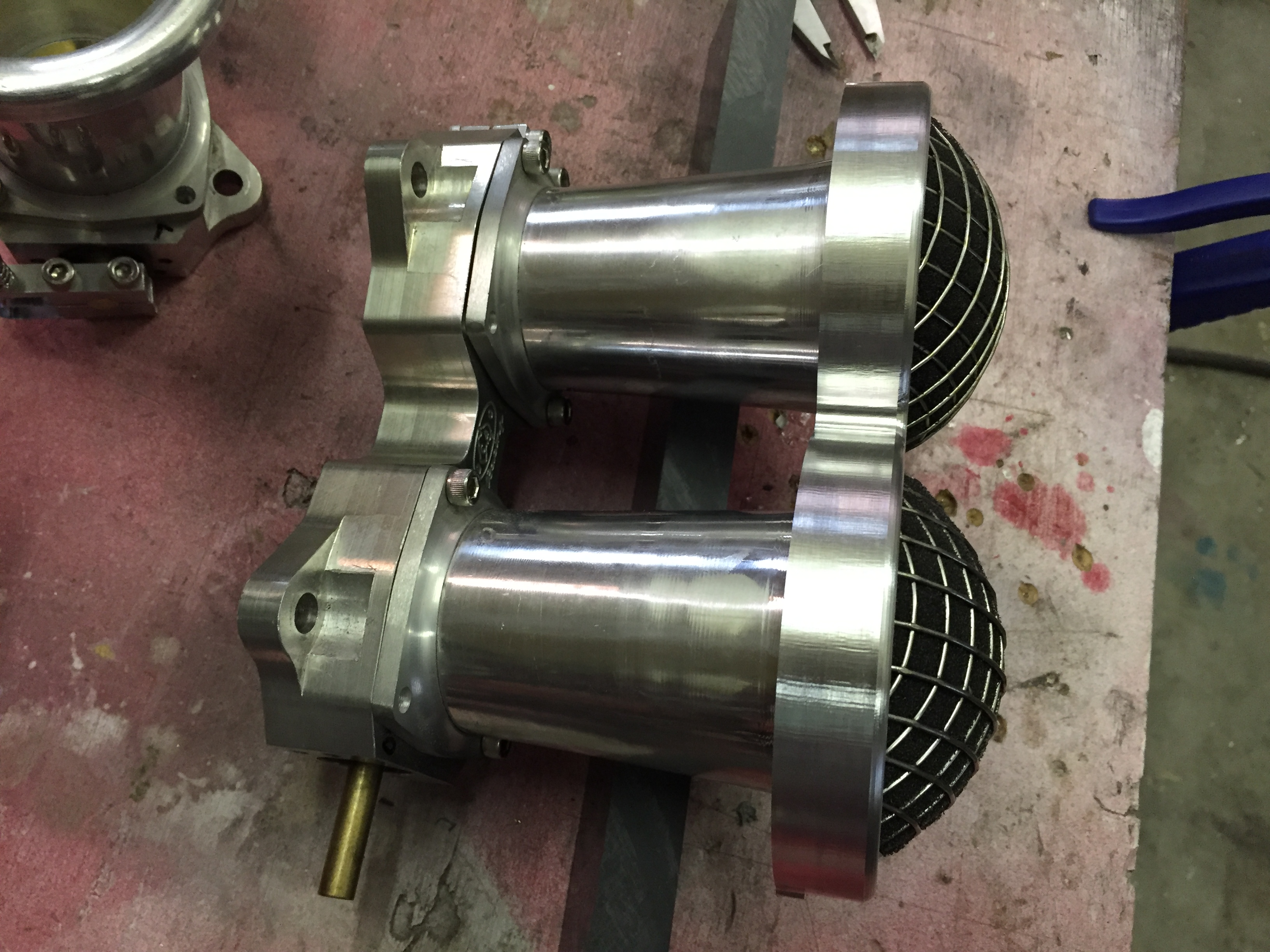
This started out as a 4″X8″X.75″ piece of 6061.
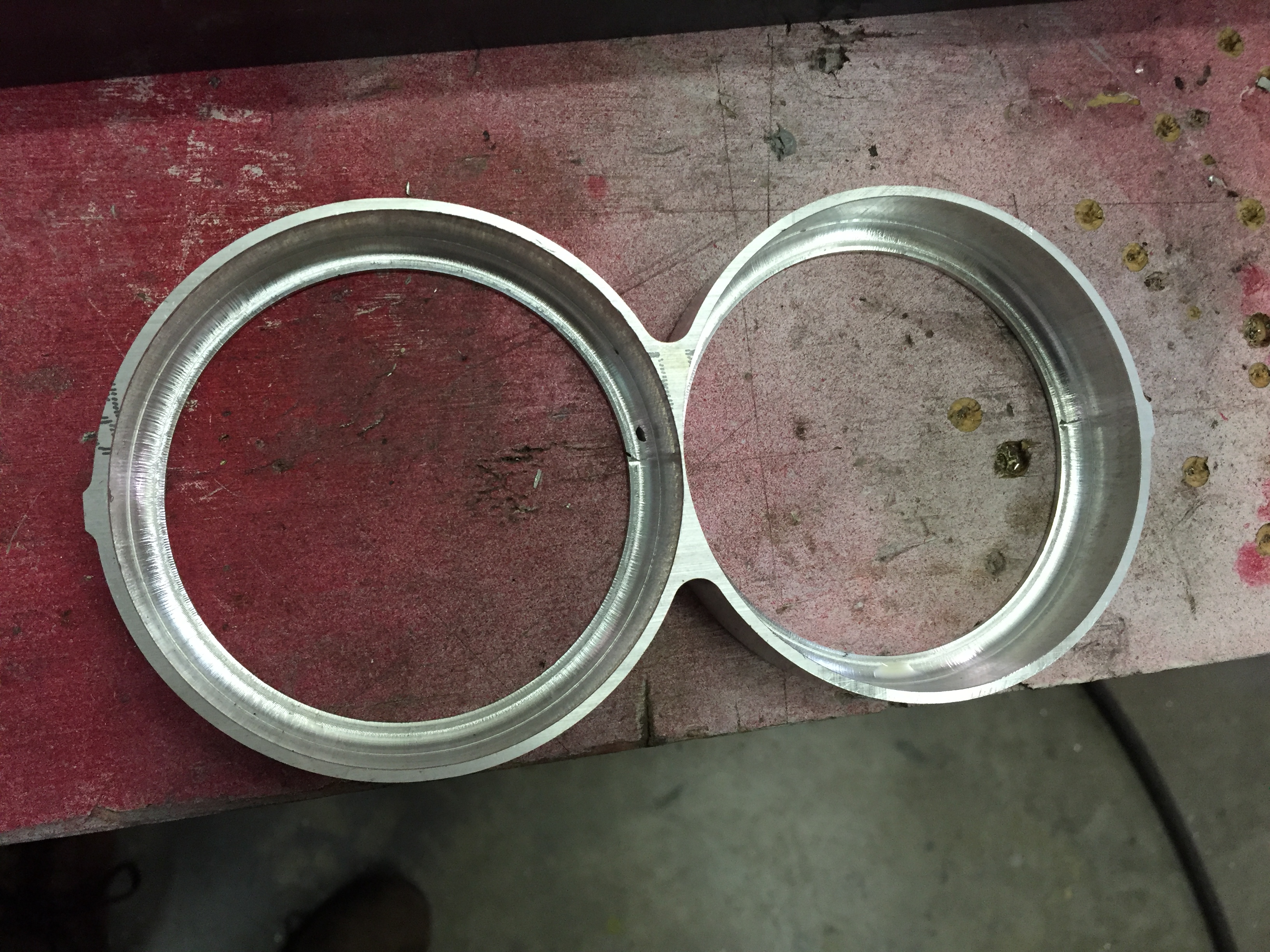
Word from Crane is I’ll have my cams by the end of next week.
Did an oil flow test and I’m getting excellent results up through the towers to the cam journals. The upper chain tensioner is getting plenty of flow as well. I won’t know beyond that until I get the cams installed.
Closer every day!