Camshaft development took place at multiple times over multiple months so I decided to condense it into one post.
I started out thinking I would call any of the Honda K20 cam mfg that offered “custom cams” on their web page and have a 6 cylinder version of one of their cams made. Well custom means custom grind. If you don’t have the core then they cant do the grind. So I went in search of having custom cam cores produced. There aren’t too many core manufacturers out there and even fewer that will talk to a privateer like me. The best price I got was like $2800.00 for 2 cams if I bought them in quantities of 8. And this was just for the core. It would still have to be final ground.
I then proceeded to educate myself about cores. I indirectly work with a steel foundry that pours 8625 steel. I decided to give that a try. I made a set of patterns and had 2 sets of cams cast. I wasn’t happy with the results. I discussed the issues with the foundry and ordered another set. While I was waiting I started to listen to all the people on HybridZ that recommended I machine my own cores out of 8620 round stock. I bit the bullet and ordered a 20 foot length of 2″ round.
Before and after. From 22 lbs down to 7 lbs
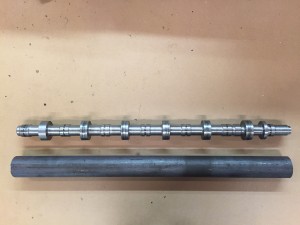
Started out by turning down the entire OD and then The back end
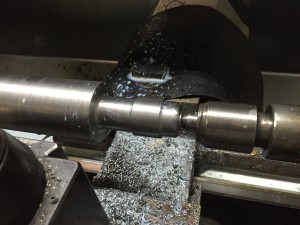
Then I flipped it around and started a carvin!
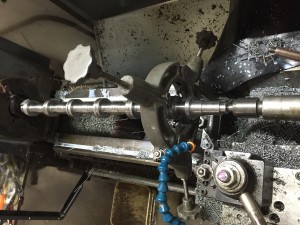
Next up will be cutting the lobes in my mill